This is why teslas stainless steel cybertrucks may be rusting – This Is Why Tesla’s Stainless Steel Cybertrucks May Be Rusting: It’s the question buzzing around the electric vehicle world. The Cybertruck, with its futuristic, stainless steel exoskeleton, promised unparalleled durability. But reports of rust are emerging, raising eyebrows and prompting questions about the material science, manufacturing processes, and even Tesla’s quality control. Let’s dive deep into the reasons behind this unexpected corrosion.
From the unique properties of the stainless steel itself—its composition, its susceptibility to environmental factors like saltwater and extreme temperatures, and the crucial role of its protective passivation layer—to the Cybertruck’s design and manufacturing processes, we’ll explore every angle. We’ll examine reports from Cybertruck owners, analyze Tesla’s official responses, and even speculate on the long-term implications for the vehicle’s structural integrity, resale value, and Tesla’s reputation. Get ready for a deep dive into the surprisingly rusty reality of the future.
Stainless Steel Properties and Rusting
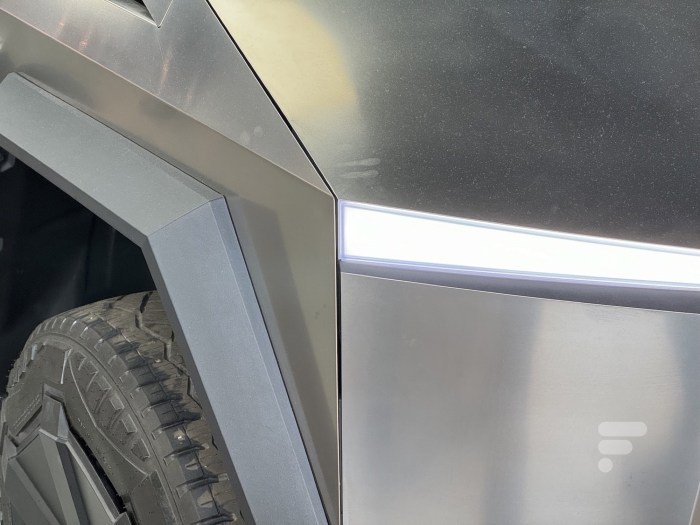
Source: frandroid.com
Tesla’s stainless steel Cybertruck rust woes? It’s not just about the metal; surface imperfections and inconsistencies in the manufacturing process play a huge role. Think about the level of precision needed – data analysis on this scale often relies on platforms like remotasks ai expert data labor , which highlights the complexity involved in quality control.
Ultimately, even with high-tech materials, consistent, high-quality manufacturing is key to preventing rust.
The Cybertruck’s much-discussed stainless steel exoskeleton, while promising durability, has sparked concerns regarding its susceptibility to rust. Understanding the intricacies of stainless steel’s corrosion resistance is crucial to assessing these concerns. This exploration delves into the material science behind the Cybertruck’s construction and the environmental factors that might compromise its longevity.
The Cybertruck utilizes a cold-rolled, austenitic stainless steel, likely a variant of 30X series stainless steel, known for its high strength and corrosion resistance. This type of stainless steel achieves its corrosion resistance primarily through its chromium content. Chromium reacts with oxygen in the air to form a passive chromium oxide layer (Cr₂O₃) on the steel’s surface. This incredibly thin, self-healing layer acts as a barrier, preventing further oxidation and thus, rust. The exact composition of the alloy used by Tesla remains proprietary, but it’s safe to assume a high percentage of chromium is present, along with nickel and possibly molybdenum to enhance its properties.
Environmental Factors Affecting Stainless Steel Corrosion
Several environmental factors can compromise the passivation layer and accelerate rusting in even the most corrosion-resistant stainless steels. Prolonged exposure to saltwater, for instance, can disrupt the protective oxide layer due to the high chloride ion concentration in seawater. These chloride ions can penetrate the passive layer, leading to pitting corrosion, a localized form of rusting. Similarly, exposure to industrial pollutants containing sulfur dioxide or other corrosive chemicals can damage the protective layer. Extreme temperatures, both high and low, can also stress the steel, making it more vulnerable to corrosion. High temperatures can accelerate oxidation processes, while extremely low temperatures can cause embrittlement, reducing the steel’s resistance to cracking and corrosion.
Comparison with Other Automotive Stainless Steels
While the exact grade of stainless steel used in the Cybertruck remains undisclosed, it’s likely a higher grade than many automotive-grade stainless steels commonly used for trim pieces or exhaust systems. These generally contain less chromium and other alloying elements, offering lower corrosion resistance. The Cybertruck’s stainless steel is intended for structural applications, requiring significantly higher strength and corrosion resistance than those used in less demanding applications. The superior corrosion resistance of the Cybertruck’s steel is expected, but the extent of this resistance under real-world conditions remains to be fully seen.
Passivation Layer and its Compromise
The passivation layer, that crucial chromium oxide film, is the key to stainless steel’s corrosion resistance. However, this layer isn’t invincible. Scratches, abrasions, and other surface damage can disrupt the layer, exposing the underlying steel to oxidation. Similarly, chemical attack from aggressive environments can dissolve the passive layer, initiating corrosion. Furthermore, improper cleaning or the presence of certain contaminants can also interfere with the formation and maintenance of the passivation layer. The self-healing nature of the layer means minor damage might repair itself, but significant or persistent damage will lead to accelerated rusting.
Cybertruck Design and Manufacturing
The Cybertruck’s ambitious design, featuring its distinctive exoskeleton of cold-rolled stainless steel, presents unique manufacturing challenges and potential vulnerabilities to corrosion. Unlike traditional automotive body construction, the Cybertruck’s manufacturing process and material choices introduce factors that could significantly impact its long-term durability and rust resistance.
The manufacturing process relies heavily on large, precisely cut stainless steel panels that are joined together. This differs from the more common method of stamping and welding numerous smaller panels, a process which allows for more controlled seam welding and easier access to areas that may trap moisture.
Manufacturing Process and Corrosion Vulnerability
The Cybertruck’s body panels are reportedly formed from massive sheets of cold-rolled stainless steel, likely using a combination of techniques including laser cutting and possibly large-scale bending processes. The inherent difficulty in precisely shaping such large panels increases the potential for microscopic imperfections or stress points in the final product. These flaws can act as nucleation sites for corrosion, particularly if they trap water or contaminants. Furthermore, the relatively fewer joins compared to a conventionally built vehicle does not necessarily mean fewer corrosion risks; rather, the potential consequences of failure at these joins are magnified. A compromised weld on a large panel could lead to more extensive damage than multiple smaller weld failures on a conventionally constructed vehicle.
Potential Water and Contaminant Accumulation Areas
Several design features on the Cybertruck could contribute to water or contaminant accumulation. The sharp angles and tight tolerances between panels create crevices where water can collect and stagnate. The design also lacks traditional body cavities and underbody panels found in most vehicles, which typically help to direct water away from critical components. Additionally, the exposed undercarriage and relatively simple design may allow for greater exposure to road salt, mud, and other corrosive elements. Consider, for example, the wheel wells—their relatively open design, compared to more enclosed wheel wells in conventional vehicles, increases the risk of water and debris buildup.
Welding and Joining Techniques and Rust Susceptibility, This is why teslas stainless steel cybertrucks may be rusting
The welding process used to join the Cybertruck’s large stainless steel panels is critical to its corrosion resistance. Improper welding techniques, such as insufficient penetration or the formation of weld spatter, can create weak points and stress concentrations that promote rust. The type of welding employed—whether it is laser welding, resistance spot welding, or another method—also influences the integrity and longevity of the welds. Any flaws in the welding process will compromise the structural integrity and, critically, leave areas vulnerable to corrosion. Furthermore, the lack of traditional sealant applications commonly used in automotive manufacturing to protect welds could exacerbate the issue.
Quality Control Issues and Corrosion Resistance
Reports of inconsistent panel fit and finish on some early Cybertruck models suggest potential quality control challenges during the manufacturing process. These imperfections, such as gaps between panels or uneven surfaces, could allow water ingress and accelerate corrosion. Even slight variations in the panel alignment can create stress points and hinder the effectiveness of any protective coatings applied to the vehicle. While the stainless steel itself offers inherent corrosion resistance, inconsistencies in manufacturing can significantly reduce its effectiveness. This is particularly concerning given the relatively large size and limited number of panels used in the Cybertruck’s construction. Any manufacturing defect is magnified by the scale of the panels.
Owner Experiences and Reports: This Is Why Teslas Stainless Steel Cybertrucks May Be Rusting
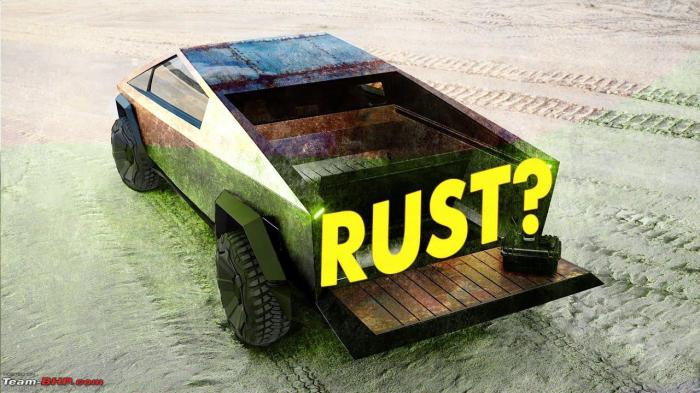
Source: team-bhp.com
Anecdotal evidence from Cybertruck owners paints a complex picture regarding rust susceptibility. While Tesla marketed the stainless steel construction as virtually impervious to corrosion, reports of rusting have emerged from various corners of the globe, challenging this initial claim. These reports offer valuable insights into the real-world performance of the Cybertruck’s exterior and highlight potential manufacturing or design flaws.
The emergence of rust on a vehicle touted for its corrosion resistance is naturally a cause for concern among owners and observers alike. Understanding the patterns and severity of reported rust issues is crucial for assessing the long-term durability of the Cybertruck and informing potential buyers. Analyzing these reports, categorized by location and affected area, allows us to identify potential contributing factors.
Reported Rust Occurrences by Location and Affected Area
Several online forums and social media platforms dedicated to Tesla vehicles showcase images and discussions about rust on Cybertrucks. Reports indicate that rust is not uniformly distributed across all vehicles, suggesting a potential link between environmental factors and the development of corrosion.
Location | Affected Area | Severity | Possible Cause |
---|---|---|---|
Coastal California, USA | Lower door panels, wheel wells | Moderate; surface rust | Saltwater exposure, insufficient protective coating |
Texas, USA | Rear bumper, tailgate | Mild; superficial pitting | Exposure to harsh sun and dust; potential manufacturing defect |
Norway | Undercarriage | Severe; significant corrosion | Road salt application during winter months |
Arizona, USA | Seam welds | Mild; minor surface rust | Imperfect weld sealing, allowing moisture penetration |
Visual Representation of Rust Locations
Imagine a Cybertruck viewed from the side. A visual representation of typical rust locations would highlight several key areas. The lower sections of the body, particularly the door panels and wheel wells, often show signs of rust. This is likely due to increased exposure to road spray, salt, and other corrosive elements. The rear bumper and tailgate are also vulnerable areas, potentially due to less effective protection during manufacturing or increased exposure to environmental factors. Finally, some reports indicate rust appearing around seam welds, suggesting that moisture might be penetrating these joints. The visualization would use a color-coded overlay, with red highlighting the areas most frequently affected by rust. The intensity of the red would correspond to the severity of the rust reported in owner accounts. The undercarriage would also be indicated as a potentially vulnerable area, especially in regions with heavy road salt usage.
Tesla’s Response and Solutions
Tesla’s official stance on Cybertruck rusting remains somewhat elusive, lacking a comprehensive public statement directly addressing widespread concerns. Instead, the company’s response has been piecemeal, often relying on individual customer service interactions and indirect communication through social media and forums. This lack of a unified, transparent approach has fueled speculation and amplified customer anxieties. The situation highlights a communication gap between Tesla and its Cybertruck owners regarding a significant durability issue.
Tesla’s approach to resolving reported rust issues appears to be largely case-by-case. While there’s no publicly available, detailed repair protocol specifically for rust damage, anecdotal evidence suggests that Tesla service centers have addressed individual complaints on a need-by-need basis. This approach contrasts with the more standardized warranty processes and readily available repair information commonly provided by other automakers for similar issues. This individualized approach, while potentially flexible, also lacks the transparency and predictability of a formalized procedure.
Tesla’s Warranty Coverage for Rust Damage
Tesla’s standard new vehicle warranty likely covers manufacturing defects, including potential flaws in the stainless steel that could lead to premature rusting. However, the specifics regarding rust damage coverage are not explicitly detailed in publicly available warranty documents. This ambiguity leaves customers uncertain about the extent of their protection against rust-related repairs. The lack of clear guidelines contrasts with many competitors who offer specific corrosion warranties, outlining conditions and limitations for coverage. For example, some manufacturers offer a “perforation warranty” covering rust that penetrates the body panels, whereas others provide a more comprehensive “corrosion warranty” that may cover surface rust as well. The absence of similar clear language from Tesla leaves Cybertruck owners in a vulnerable position regarding potential repair costs.
Comparison with Other Manufacturers’ Approaches
Unlike Tesla’s seemingly reactive approach, established automakers often proactively address potential rust issues through robust preventative measures and detailed warranty policies. These measures can include specialized coatings, advanced materials resistant to corrosion, and clearly defined warranty clauses specifying coverage for rust damage. For instance, many manufacturers utilize zinc-coated steel, known for its superior rust resistance, in their vehicle construction. They often also provide detailed guides for owners on proper vehicle maintenance to minimize the risk of rust, including recommendations for cleaning and care specific to their vehicle’s materials. Tesla’s current lack of such proactive measures and transparent warranty information creates a stark contrast with industry best practices.
Tesla’s Planned Actions to Mitigate Rusting
While Tesla hasn’t announced any widespread preventative measures or design changes to address Cybertruck rusting, the ongoing case-by-case repairs suggest an implicit acknowledgement of the problem. However, the absence of a public commitment to implement broader solutions, such as revised materials or manufacturing processes, leaves many wondering about the long-term durability of the vehicle. The company’s silence on potential future improvements raises concerns about whether Tesla plans to address the underlying causes of the reported rusting, or if the current approach of individual repairs will remain the standard response. A proactive approach, involving public announcements and potential recalls or upgrades, would likely improve customer confidence and align Tesla’s practices with industry norms.
Future Implications and Predictions
The rusting issues plaguing some Tesla Cybertrucks represent more than just a cosmetic problem; they pose significant long-term implications for the vehicle’s structural integrity, resale value, and Tesla’s overall brand image. Understanding these potential consequences is crucial for both current owners and prospective buyers, as well as for Tesla’s future product development.
The potential for widespread corrosion could severely compromise the Cybertruck’s structural integrity over time. This stainless steel exoskeleton, while initially touted for its durability, might become weakened by rust, potentially affecting its crashworthiness and overall safety. Furthermore, the diminished structural integrity could lead to costly repairs, impacting the vehicle’s lifespan and reducing its overall value.
Long-Term Effects on Resale Value and Structural Integrity
The emergence of rust on a vehicle typically signifies significant depreciation. Consider the classic example of early-model Jeep Wranglers, where rust was a common issue, leading to dramatically reduced resale values. A similar scenario could unfold with the Cybertruck if rust problems prove widespread and difficult to resolve. The combination of structural compromise and diminished aesthetic appeal could severely impact the vehicle’s market value, potentially leaving owners with significant financial losses. This is especially true given the Cybertruck’s relatively high initial purchase price. The impact extends beyond individual owners; it could also influence the used car market as a whole, potentially depressing the value of existing and future Cybertrucks.
Impact on Tesla’s Reputation and Future Designs
The Cybertruck rust issue presents a significant challenge to Tesla’s reputation for innovation and quality. The company has cultivated an image of producing cutting-edge vehicles, and the emergence of a significant manufacturing or design flaw—especially one as visible as rust—could damage this carefully constructed image. This could affect consumer confidence in future Tesla models, potentially leading to decreased sales and impacting the company’s overall market share. The negative publicity surrounding the issue could also discourage potential investors and harm Tesla’s brand value in the long term. Learning from this experience, Tesla needs to demonstrate proactive measures to prevent similar issues in future vehicle designs. The handling of this situation will be a key test of the company’s ability to manage and resolve significant quality control problems.
Hypothetical Cost of Addressing Widespread Rust Issues
Let’s imagine a worst-case scenario: 50% of the Cybertrucks produced experience significant rust issues requiring extensive bodywork repairs. Assuming an average repair cost of $10,000 per vehicle (a conservative estimate given the complexity of the Cybertruck’s body), the total cost for Tesla to address this issue could reach billions of dollars. This figure doesn’t include the cost of potential lawsuits, warranty claims, and the negative impact on brand reputation. This hypothetical scenario highlights the potentially catastrophic financial implications of failing to address the rust problem effectively. The scale of such a recall would be unprecedented in the automotive industry, impacting not only Tesla’s financial stability but also the confidence of investors and consumers alike.
Mitigating Future Rust Problems Through Design and Manufacturing Improvements
To prevent similar issues in future vehicles, Tesla could implement several improvements. This might include utilizing different grades of stainless steel with enhanced corrosion resistance, improving the vehicle’s protective coatings, or refining the manufacturing process to minimize surface imperfections that can accelerate rust formation. Implementing more rigorous quality control checks throughout the production process, from raw material selection to final assembly, is crucial. Furthermore, designing the vehicle with better drainage systems to prevent water accumulation in vulnerable areas could significantly reduce the risk of rust. Lessons learned from the Cybertruck’s rust problems can inform the design and manufacturing processes of future Tesla vehicles, preventing similar issues and reinforcing the company’s commitment to quality and durability.
Conclusive Thoughts

Source: jazelc.com
The rusting Cybertruck saga isn’t just a cosmetic issue; it’s a complex interplay of material science, manufacturing, and environmental factors. While Tesla’s stainless steel choice aimed for unparalleled durability, the reality reveals vulnerabilities. The ongoing reports highlight the importance of rigorous quality control, and the potential long-term consequences for both vehicle owners and Tesla’s brand image. Whether Tesla’s solutions prove effective remains to be seen, but one thing’s clear: the Cybertruck’s rusting issues have opened a Pandora’s Box of questions about the marriage of cutting-edge design and real-world durability.